El moldeo por inyección es uno de procesos más eficientes en la fabricación de piezas de plástico. Evitar imperfecciones y defectos en las piezas finales, sin embargo, requiere de un alto grado de experiencia técnica.
Incluso errores pequeños en las primeras fases del proceso pueden generar problemas importantes o comprometer la integridad del producto. Debes tener en cuenta que los defectos en las piezas elaboradas con moldeo por inyección pueden:
- Reducir la rentabilidad de todo el proceso
- Reducir la velocidad de producción
- Acortar la vida útil de los productos inyectados
Algunos de los defectos más comunes que pueden ocurrir en el moldeo por inyección de plástico son:
-
Líneas de flujo
Las líneas de flujo son patrones descoloridos en una pieza, causados por el movimiento variable del plástico fundido en el molde de inyección. Esto indica velocidades o presiones de inyección insuficientes.
También pueden aparecer líneas de flujo cuando la resina termoplástica se mueve a través de partes del molde con diferentes espesores de pared.
Solución
Mantén un espesor de pared constante y asegúrate de que los chaflanes y filetes tengan la longitud adecuada. Colocar la compuerta en una sección de paredes delgadas de la cavidad de la herramienta puede ayudar aún más a reducir las líneas de flujo.
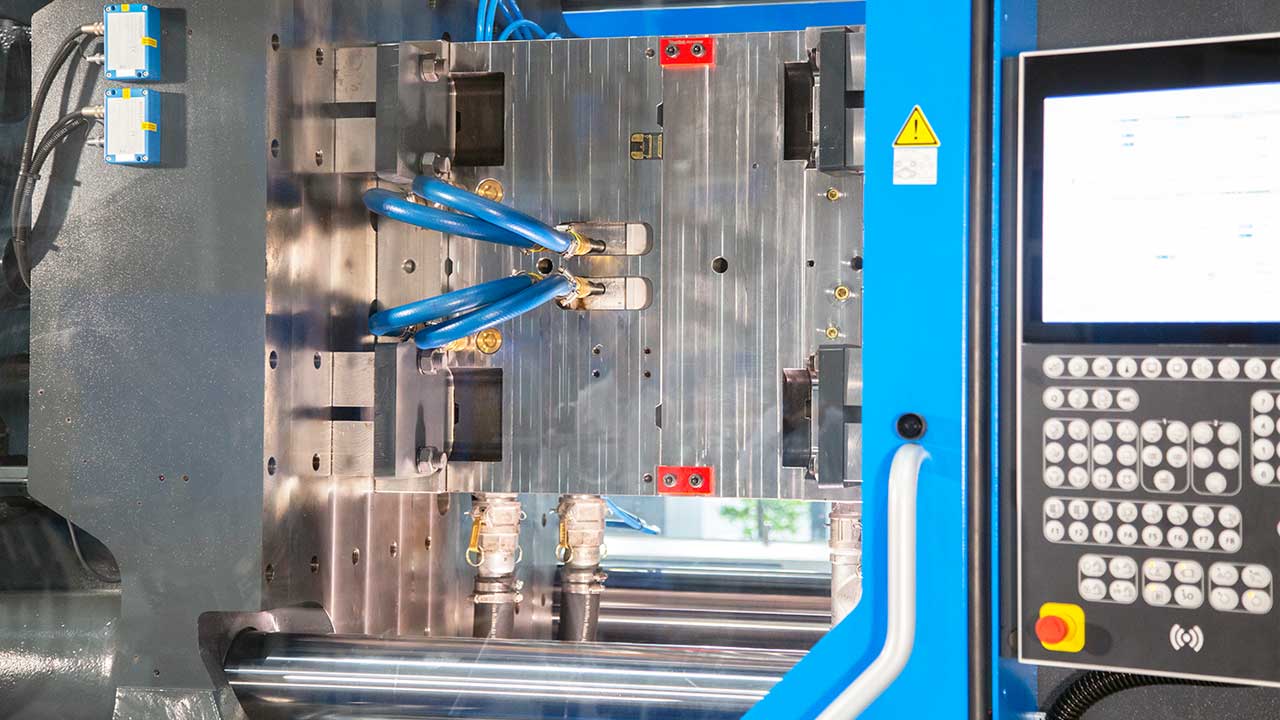
-
Marcas de hundimiento
Aparecen como depresiones, abolladuras o cráteres en secciones gruesas de una pieza. Las secciones más gruesas tardan más en enfriarse, lo que puede tener el efecto secundario a menudo inesperado de que las partes internas de la pieza se contraigan a un ritmo muy diferente al de las secciones externas.
Solución
Estas marcas suelen ser un indicador de que el plástico necesita más tiempo dentro del molde para enfriarse y curarse adecuadamente. Se pueden evitar reduciendo el grosor de las secciones de pared más gruesas, lo que ayuda a garantizar un enfriamiento más uniforme y completo. Una presión inadecuada en la cavidad del molde o temperaturas superiores a las deseables en la puerta también pueden contribuir al desarrollo de defectos.
También lee: Tres consejos para mejorar el moldeo por inyección
-
Líneas de soldadura
Estos defectos dejan una marca en el lugar en el que dos o más flujos de resina fundida se unieron y solidificaron en un punto del molde. Son el resultado de temperaturas inadecuadas que provocan que los dos flujos no se unan correctamente, lo que provoca una línea visible.
Solución
Las líneas de soldadura reducen la resistencia y la durabilidad de los componentes, por lo que se recomienda aumentar la temperatura de la resina fundida para evitar que el proceso de solidificación inicie demasiado pronto.
Aumentar la velocidad y la presión de inyección también reduce el riesgo de aparición de líneas de soldadura.
-
Alabeo
Es una deformación (warpage) en la geometría de las piezas que puede ser el resultado de diferencias térmicas y/o presiones de contacto. Otras causas comunes suelen ser o diferentes espesores de pared, la posición de las entradas y dimensiones o diferentes velocidades de enfriamiento, entre otras.
Solución
Asegúrate de contar con un buen diseño de pieza en el que se reduzcan los cambios bruscos en la sección transversal. Se recomienda contar con un buen atemperamiento en el molde que garantice una remoción eficiente de energía.
Es clave evitar los puentes en canales de enfriamiento largos, ya que el agua puede calentarse en el recorrido dentro del molde y se reducir la eficiencia local de enfriamiento, provocando gradientes térmicos.
-
Delaminación de la superficie
La delaminación es una condición que hace que la superficie de una pieza se separe en capas delgadas. Estas capas, que parecen recubrimientos que se pueden despegar, se deben a la presencia de contaminantes en el material que no se adhieren al plástico, generando fallas localizadas.
Solución
Aumenta la temperatura del molde y adaptar el mecanismo de expulsión del molde para que dependa menos de los agentes desmoldantes, ya que estos agentes pueden aumentar el riesgo de delaminación. También puede ser útil secar previamente adecuadamente el plástico antes de moldearlo.
-
Partes incompletas
Son secciones de las piezas moldeadas que no se han llenado completamente o que presentan vacíos, huecos o áreas no conformes. Pueden ser resultado de una velocidad de inyección demasiado baja, de obstrucciones de la boquilla o de falta de material suficiente en la tolva.
Solución
Inyectar más material y/o aumentar la velocidad de inyección puede ser una solución simple a este problema. También se recomienda cambiar el molde a una máquina de mayor capacidad de ser posible.
Evita defectos en el moldeo por inyección
Para evitar estos y otros errores es necesario un monitoreo constante del proceso, mantener la maquinaria en buen estado, realizar un mantenimiento regular de los moldes y ajustar adecuadamente los parámetros del proceso.